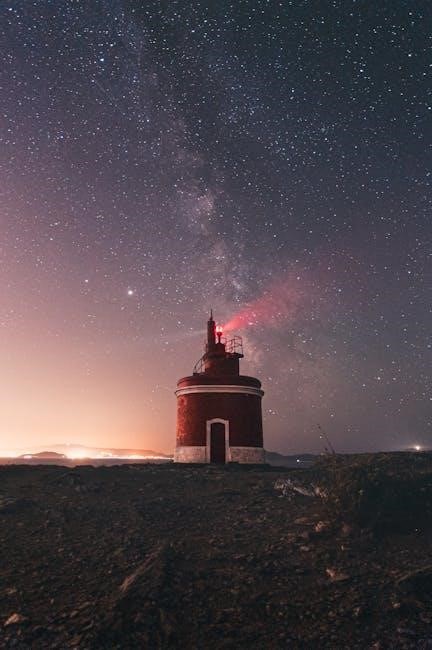
LM Guides‚ developed by THK‚ are linear motion components enabling smooth‚ precise movement in machinery. They use rolling elements like balls or rollers‚ ensuring high rigidity and energy efficiency‚ and are crucial in industrial automation and robotics.
1.1 Overview of LM Guides
LM Guides are linear motion components designed for smooth‚ precise movement in machinery. They utilize rolling elements like balls or rollers‚ ensuring high precision‚ rigidity‚ and energy efficiency. These guides are essential in industrial automation‚ robotics‚ and machine tools‚ offering long service life and reliability in various applications.
1.2 History and Development of LM Guides
LM Guides were first introduced by THK as the world’s first practical linear rolling motion component. Developed to meet growing industrial demands for precision and efficiency‚ they evolved to include caged ball and roller types‚ enhancing performance and enabling maintenance-free operation over time.
1.3 Importance of LM Guides in Linear Motion Systems
LM Guides are critical in linear motion systems for their ability to handle loads precisely and efficiently. They provide high rigidity‚ reduce friction‚ and enable smooth movement‚ making them essential in applications requiring accuracy‚ durability‚ and energy efficiency across various industries.
Structure and Components of LM Guides
LM Guides consist of rails and blocks with rolling elements like balls or rollers. Endplates ensure ball circulation‚ enabling smooth linear motion and high rigidity in applications.
2.1 Rails and Blocks: Key Components
LM Guides feature precision-ground rails and blocks with raceways for rolling elements. The rail provides a smooth path‚ while the block houses balls or rollers‚ ensuring precise linear motion. Durable materials like stainless steel and carbon steel enhance longevity and performance in various applications.
2.2 Rolling Elements: Balls vs. Rollers
LM Guides utilize balls or rollers as rolling elements. Balls offer low friction‚ high speed‚ and energy efficiency‚ while rollers provide higher rigidity and load capacity. The choice depends on application needs‚ with caged designs preventing ball contact and enhancing performance in both configurations.
2.3 Endplates and Ball Circulation Mechanism
Endplates in LM Guides facilitate ball circulation‚ ensuring consistent movement and load distribution. This mechanism prevents ball contact‚ reduces friction‚ and enables smooth operation. It enhances durability and maintains precision‚ allowing the system to function efficiently under varying loads and speeds.
Types of LM Guides
LM Guides are available in caged ball‚ full-ball‚ and roller-type designs‚ each offering unique benefits for specific applications‚ ensuring versatility in linear motion systems.
3.1 Caged Ball LM Guides
Caged Ball LM Guides use ball cages to reduce friction and retain grease‚ enabling low noise‚ high speed‚ and maintenance-free operation. The 45-degree contact angle allows uniform load distribution in all directions‚ making them versatile for various applications. Models like SHS and SSR exemplify this design‚ ensuring high performance and reliability in linear motion systems.
3.2 Full-Ball LM Guides
Full-Ball LM Guides feature a higher load capacity due to their full complement of balls without cages. They are ideal for heavy-duty applications requiring maximum rigidity and load-bearing capabilities. However‚ they lack the maintenance-free benefits of caged designs and require careful handling to prevent ball displacement during installation or maintenance.
3.3 Roller-Type LM Guides
Roller-Type LM Guides use cylindrical rollers instead of balls‚ offering exceptional rigidity and load capacity. They are designed for ultra-high rigidity and heavy loads‚ making them ideal for applications requiring stability under extreme conditions. These guides are particularly effective in machinery where high precision and durability are critical‚ such as in industrial automation and large-scale manufacturing.
Applications of LM Guides
LM Guides are widely used in industrial automation‚ robotics‚ and machine tools for precise linear motion. They also find applications in medical instruments and CNC machines‚ ensuring high accuracy and reliability in diverse operational environments.
4.1 Industrial Automation and Robotics
LM Guides are integral to industrial automation and robotics‚ enabling precise and smooth linear motion in applications like assembly lines‚ CNC machines‚ and robotic arms. Their high rigidity‚ load capacity‚ and low friction ensure efficient operation‚ reducing downtime and increasing productivity in automated manufacturing systems.
4.2 Machine Tools and CNC Machines
LM Guides are essential in machine tools and CNC machines‚ providing high precision and rigidity for accurate cutting and drilling. Their ability to handle heavy loads and maintain stability ensures consistent performance‚ making them critical components in high-speed and high-accuracy manufacturing operations where minimal vibration and noise are required.
4.3 Medical and Precision Instruments
LM Guides play a vital role in medical and precision instruments‚ offering high accuracy and smooth motion. Their low noise and vibration characteristics make them ideal for sensitive applications like surgical robots‚ laboratory equipment‚ and medical imaging devices‚ where precise control and reliability are paramount to ensure patient safety and operational effectiveness.
Installation and Maintenance
Proper handling‚ storage‚ and mounting techniques are essential for LM Guides. Regular lubrication and scheduled maintenance ensure optimal performance and extend service life.
5.1 Handling and Storage Precautions
Store LM Guides horizontally in original packaging‚ avoiding extreme temperatures and humidity. Handle with care to prevent scratches or contamination. Keep blocks and rails clean‚ ensuring no exposure to dust or debris. Proper storage ensures longevity and maintains performance quality. Always follow manufacturer guidelines for handling and storage to preserve functionality and precision;
5.2 Mounting and Alignment Techniques
Mounting and aligning LM Guides requires precision. Ensure rails are clean and parallel‚ using shims or adjustment plates for alignment. Secure the block firmly‚ avoiding over-tightening. Proper alignment prevents wear and ensures smooth operation. Follow manufacturer guidelines for optimal installation and system performance.
5.3 Lubrication and Maintenance Schedule
Regular lubrication of LM Guides is essential for maintaining performance. Use high-quality grease compatible with the guide’s materials. Re-lubrication intervals depend on operational conditions‚ such as load‚ speed‚ and environment. Clean the guide before applying grease to prevent contamination. Proper maintenance extends service life and ensures smooth‚ quiet operation.
Selection Criteria for LM Guides
Choosing LM Guides involves evaluating load capacity‚ precision needs‚ speed‚ and environmental factors. Proper selection ensures optimal performance‚ longevity‚ and reliability in diverse applications.
6.1 Load Capacity and Precision Requirements
Load capacity and precision are critical when selecting LM Guides. Caged ball and full-ball types offer varying load capacities‚ while precision levels ensure minimal deflection. Higher-rated models suit heavy-duty applications‚ ensuring stability and accuracy in industrial automation and machine tools.
6.2 Speed and Acceleration Considerations
Speed and acceleration requirements influence LM Guide selection. High-speed models‚ like the HSR series‚ are designed for rapid movement with minimal vibration. Proper lubrication and maintenance ensure optimal performance at higher velocities‚ preventing wear and tear‚ and maintaining operational efficiency in demanding applications.
6.3 Environmental and Operational Factors
Environmental conditions such as temperature‚ humidity‚ and contamination impact LM Guide performance. Stainless steel models‚ like the HSR stainless series‚ are ideal for harsh environments. Proper sealing and protective covers prevent dust and moisture ingress‚ ensuring reliability in tough operational settings and extending service life.
Key Features and Benefits
LM Guides offer high precision‚ rigidity‚ and energy efficiency‚ with low noise operation. Their robust design ensures long service life‚ making them ideal for high-speed‚ heavy-duty applications across various industries.
7.1 High Precision and Rigidity
LM Guides deliver exceptional precision and rigidity through their advanced ball or roller contact systems. The 45-degree ball contact angle ensures uniform load distribution‚ enabling stable‚ high-precision motion. This design minimizes vibration and ensures consistent performance‚ making LM Guides ideal for demanding applications requiring tight tolerances and reliable operation.
7.2 Energy Efficiency and Low Noise Operation
LM Guides are engineered for energy efficiency and quiet operation. The ball cage design reduces friction between rolling elements‚ promoting smooth motion and minimal noise. This results in lower energy consumption and extended maintenance-free operation‚ making them suitable for applications requiring high performance with reduced power consumption and operational disturbances.
7.3 Long Service Life and Reliability
LM Guides are designed for long service life and reliability‚ featuring a ball circulation mechanism that prevents ball loss and ensures smooth operation. Durable materials and precise engineering minimize wear‚ while lubrication options extend maintenance intervals. This makes LM Guides highly reliable for demanding applications‚ ensuring consistent performance over time.
Comparison with Other Linear Motion Systems
LM Guides excel with rolling elements‚ reducing friction and enabling high precision. They offer superior load capacity and durability compared to linear bearings and slide guides‚ ensuring efficient performance.
8.1 LM Guides vs. Linear Bearings
LM Guides utilize rolling elements like balls or rollers for smooth motion‚ offering higher precision and load capacity. Linear bearings‚ often simpler and more affordable‚ rely on sliding elements‚ making them less precise but suitable for basic applications. LM Guides excel in high-speed‚ high-rigidity scenarios‚ while linear bearings are better for simple‚ low-demand tasks.
8.2 LM Guides vs. Slide Guides
LM Guides use rolling elements for smooth‚ low-friction motion‚ offering high precision and durability. Slide guides rely on sliding elements‚ which can cause wear and noise. LM Guides excel in high-precision‚ high-load applications‚ while slide guides are simpler and cost-effective for basic linear motion needs with lower performance requirements.
Accessories and Options
Accessories like lubrication units‚ protective covers‚ and seals enhance LM Guide performance. Customization options‚ including special orders‚ cater to specific application needs‚ ensuring optimal functionality and longevity.
9.1 Lubrication Units and Grease Options
Lubrication units and grease options are crucial for LM Guides‚ ensuring smooth operation and longevity. Advanced lubrication technologies enhance grease retention‚ reducing friction and noise. Maintenance-free designs‚ with ball cages‚ optimize performance in high-speed applications‚ while specialized greases cater to varying environmental conditions‚ ensuring reliability and extending service life.
9.2 Protective Covers and Seals
Protective covers and seals are essential for safeguarding LM Guides from contaminants. Durable materials and advanced designs prevent dust and debris ingress‚ ensuring optimal performance. Seals are tailored for various environments‚ from standard to harsh conditions‚ maintaining lubricant retention and minimizing wear‚ thus extending the operational lifespan of the LM Guide system.
9.3 Customization and Special Orders
Customization options for LM Guides cater to specific application needs. Special orders allow modifications in dimensions‚ materials‚ and configurations. Stainless steel variants are available for corrosion resistance. Manufacturers like THK offer tailored solutions‚ ensuring compatibility and performance in unique or demanding environments‚ making LM Guides adaptable to diverse industrial requirements and challenges.
Case Studies and Examples
LM Guides are widely used in industrial automation‚ robotics‚ and medical devices‚ showcasing their reliability and precision. Real-world applications demonstrate their ability to enhance machine performance‚ ensuring smooth and efficient linear motion across various industries.
10.1 Successful Applications in Various Industries
LM Guides are integral to industrial automation‚ robotics‚ and CNC machines‚ ensuring high precision and reliability. They also find applications in medical instruments‚ where smooth‚ accurate motion is critical. Their versatility and durability make them essential in diverse sectors‚ driving innovation and efficiency in manufacturing and precision engineering systems globally.
10.2 Real-World Performance and Results
LM Guides deliver exceptional performance‚ achieving high-speed operations with minimal noise. In industrial settings‚ they enhance productivity and reduce downtime. Medical devices benefit from their precise motion‚ while robotic systems achieve smoother‚ more accurate movements. Their durability and low maintenance requirements result in long-term cost savings across various applications. Results consistently exceed expectations.
Troubleshooting and Common Issues
Common issues with LM Guides include noise‚ vibration‚ and wear. Proper installation‚ lubrication‚ and alignment are critical. Regular maintenance and inspection ensure optimal performance and longevity.
11.1 Common Mistakes in Installation
Common installation errors include improper alignment‚ insufficient lubrication‚ and incorrect mounting orientation. These mistakes can lead to uneven load distribution‚ noise‚ and premature wear. Proper handling and storage‚ as outlined in THK guidelines‚ are essential to prevent these issues and ensure optimal LM Guide performance and longevity in applications.
11.2 Diagnosing Wear and Tear
Wear and tear on LM Guides can be identified through increased noise‚ vibration‚ or play. Regular inspections should check for ball or roller damage‚ rail wear‚ and lubrication levels. Early detection prevents further damage‚ ensuring prolonged service life and maintaining system efficiency and precision in linear motion applications.
11.3 Solutions for Noise and Vibration
Noise and vibration in LM Guides can be addressed by ensuring proper lubrication‚ checking alignment‚ and verifying ball circulation. Regular maintenance‚ including grease replenishment‚ helps minimize friction. Proper installation and alignment techniques also reduce vibration. Using caged ball designs prevents ball-to-ball contact‚ further reducing noise and ensuring smoother operation;
LM Guides revolutionize linear motion with high precision‚ rigidity‚ and energy efficiency. Future trends focus on advancing materials and smart technologies‚ enhancing performance and sustainability in industrial applications.
12.1 Summary of LM Guide Benefits
LM Guides offer high precision‚ rigidity‚ and energy efficiency‚ enabling smooth linear motion. Their rolling elements reduce friction‚ allowing for high-speed operation and long service life. Suitable for diverse applications‚ they enhance machine performance and durability‚ making them indispensable in industrial automation and robotics.
12.2 Emerging Trends in Linear Motion Technology
Emerging trends in linear motion technology include advanced materials like stainless steel for durability‚ compact designs for space efficiency‚ and integration of IoT for real-time monitoring. Innovations in roller and ball cage systems enhance speed and precision‚ while maintenance-free options reduce downtime‚ driving smarter‚ high-performance solutions across industries.