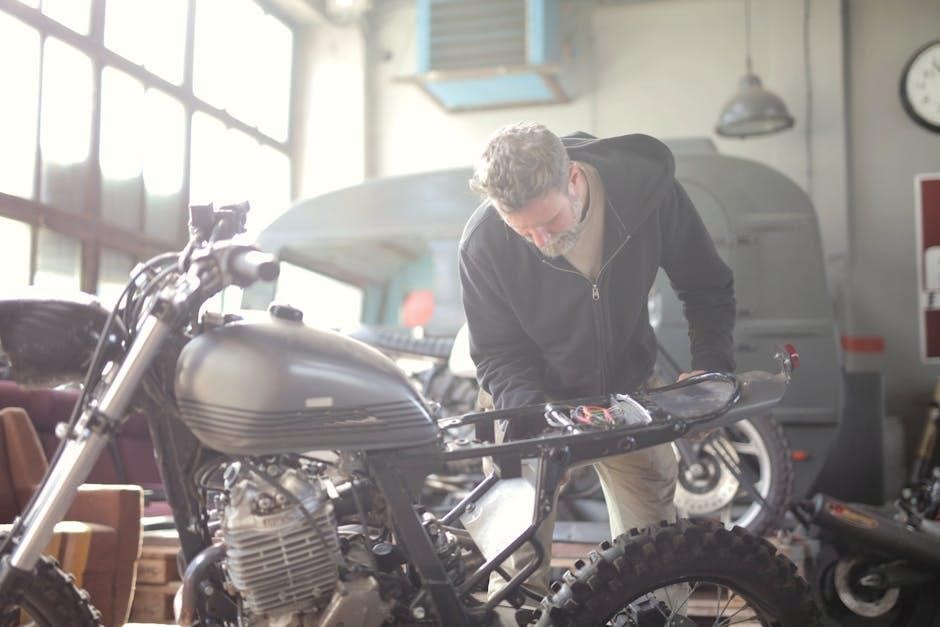
CNC machine manuals are comprehensive guides detailing safety guidelines, programming basics, machine setup, operation, and troubleshooting. They are essential for understanding and effectively operating CNC milling machines, ensuring precision and efficiency in machining processes.
1.1 Understanding the Importance of CNC Manuals
CNC manuals are crucial for safe and efficient machine operation. They provide detailed guidance on programming, safety protocols, and troubleshooting, ensuring precise machining. These manuals help operators understand machine components, optimize processes, and maintain equipment. They are essential for both beginners and experienced professionals to maximize productivity and prevent errors or accidents. Adhering to manual instructions ensures compliance with industry standards and prolongs machine longevity.
1.2 Overview of CNC Machine Components
CNC machines consist of key components like control panels, servo motors, spindle units, and cutting tools. The axis system (X, Y, Z) enables precise movement, while drives and encoders ensure accuracy. These components work together to execute programmed instructions, facilitating operations like drilling and milling. Understanding these parts is essential for effective operation, maintenance, and troubleshooting, ensuring optimal performance and safety.
Safety Precautions and Best Practices
Safety precautions are critical when working with CNC machines. Always follow manual guidelines, wear protective equipment, and ensure proper training. This section outlines essential protocols to prevent accidents, ensuring both operator and machine safety during operations.
2.1 General Safety Guidelines for CNC Machines
Safety guidelines for CNC machines emphasize operator protection. Always wear protective equipment, including safety glasses and gloves. Ensure loose clothing or jewelry is secured. Keep the work area clean and clear of obstacles. Avoid reaching into the machining area while the machine is operational. Familiarize yourself with the machine-specific safety manual and understand DANGER, WARNING, and CAUTION notifications to prevent accidents and ensure safe operation.
2.2 Handling Machine-Specific Safety Protocols
Machine-specific safety protocols vary by manufacturer and model. Always refer to the CNC machine’s manual for detailed instructions. Understand and follow lockout/tagout procedures to prevent unexpected startups. Be aware of emergency stop locations and know when to use them. Regularly inspect safety features like guards and interlocks. Adhere to manufacturer guidelines for maintenance and repairs to ensure compliance and operator safety. Never bypass safety mechanisms without authorization.
Programming Basics for CNC Mills
CNC milling involves mastering G-Code and M-Code programming. These codes guide the machine’s movements, ensuring precise cuts and efficient operations. Understanding fundamental programming concepts is crucial for achieving accurate results. Always follow safety protocols and verify programs before execution to avoid errors and ensure smooth machining processes.
3.1 G-Code and M-Code Fundamentals
G-Code is the primary programming language for CNC machines, controlling axis movements and operations. M-Code manages machine functions like tool changes and coolant activation. Together, they enable precise machining. G-Code defines cutting paths, while M-Code handles auxiliary functions. Understanding these codes is essential for operators and programmers to ensure accurate and efficient operations. Always refer to the manual for manufacturer-specific code variations to avoid errors and ensure safe, effective machining.
3.2 Creating Simple CNC Programs
Creating simple CNC programs involves defining tool paths and operations using G-Code and M-Code. Start with a clear workpiece setup and input precise dimensions. Define tool offsets and sequence operations logically. Use simulation software to verify programs before machining. Include safety commands like spindle stop and tool retraction. Always test programs in a controlled environment to ensure accuracy and prevent errors, adhering to machine-specific guidelines outlined in the manual.
Machine Setup and Initialization
Machine setup and initialization involve calibrating axes, setting tool offsets, and verifying program parameters. Ensure all components are aligned and configured according to the manual for accurate operation.
4.1 Initial Setup and Calibration
Initial setup involves powering up the machine, initializing the control system, and setting tool lengths. Calibration ensures precise axis alignment and accurate positioning. Reference workpieces and tools, and verify all parameters before operation to guarantee optimal performance and safety. Proper setup is critical for achieving desired machining results and preventing errors.
4.2 Loading and Verifying Programs
Loading programs involves transferring CNC code to the machine via USB, network, or direct input. Verify programs by checking syntax, tool paths, and coordinates. Run simulations to ensure operations are error-free and align with design specifications. This step ensures safe and accurate machining, preventing costly mistakes and downtime. Always confirm program compatibility with the machine’s control system before execution.
Operating the CNC Machine
Operating a CNC machine involves starting and monitoring machining operations, ensuring safety and efficiency. Follow manual guidelines for drilling, milling, and other processes to achieve precise results.
5.1 Starting and Monitoring Machining Operations
Starting a CNC machine involves powering on the system, loading the verified program, and initializing the spindle and axis motors. Ensure all safety precautions are met before cycle start. Monitor the machining process through the control panel, observing tool paths and operation sequences. Use diagnostic screens to track progress and address any alarms or errors promptly. Continuous monitoring ensures precision, safety, and efficiency in production.
5.2 Handling Common Operations like Drilling and Milling
Drilling and milling are fundamental CNC operations. Drilling uses tools like twist drills or spade drills for hole creation, while milling employs end mills or face mills for material removal. Ensure proper tool selection and setup before initiating these operations. Use G-code commands such as G81 for drilling cycles and G01 for milling paths. Always verify programs and maintain safe operating practices to achieve precise and efficient results.
Diagnostics and Troubleshooting
Diagnostics involve identifying common errors and alarms, such as tool path deviations or system malfunctions. Troubleshooting requires verifying program accuracy, analyzing alarm codes, and addressing mechanical issues promptly to ensure smooth CNC operations.
6.1 Identifying Common Errors and Alarms
Common errors in CNC machines include tool path deviations, axis overload, and program syntax issues. Alarms such as system faults or tool breakage require immediate attention. Operators must analyze error codes, review program logic, and check machine status to diagnose issues. Proactive monitoring of alarm logs and machine sensors helps prevent downtime and ensures accurate machining operations. Regular maintenance and updates minimize recurring errors, enhancing overall productivity. Always consult the manual for specific error resolutions.
6.2 Troubleshooting Techniques for CNC Mills
Troubleshooting CNC mills involves identifying error codes, reviewing program logic, and verifying machine status. Common issues include tool radius compensation errors and axis misalignment. Operators should run test programs or manual operations to isolate faults. Always check for loose connections and ensure proper tool offsets are set. Use diagnostic tools on the control panel to analyze alarm history and sensor data. Consult the manual for specific error resolutions and perform regular maintenance to prevent recurring issues.
Advanced Programming Techniques
Advanced CNC programming involves mastering G-Code and M-Code, tool radius compensation, and optimizing machining processes. These techniques enhance precision, reduce cycle times, and improve overall productivity in complex operations.
7.1 Tool Radius Compensation and Advanced G-Codes
Tool radius compensation ensures precise cutting by adjusting for tool diameter variations. Advanced G-Codes, such as G41 and G42, enable dynamic adjustments during machining. These codes simplify complex operations, reducing manual interventions and improving accuracy. Proper implementation of these techniques minimizes errors and optimizes toolpath efficiency, making them indispensable for intricate milling tasks and high-precision manufacturing processes.
7.2 Optimizing Machining Processes
Optimizing machining processes involves refining CNC programs to enhance efficiency and reduce cycle times. Techniques include feed rate adjustments, toolpath improvements, and reducing non-cutting movements. Advanced strategies like high-speed machining and adaptive milling further improve productivity. Regular tool wear monitoring and program verification ensure optimal performance, minimizing downtime and maximizing output quality in CNC operations.
Maintenance and Upkeep
Regular maintenance is crucial for extending CNC machine lifespan. Tasks include lubrication, calibration, and checking for wear. Ensure all components are clean and functioning properly to prevent operational issues.
8.1 Regular Maintenance Tasks
Regular maintenance ensures optimal CNC machine performance. Tasks include checking and replacing air filters, inspecting coolant systems, and verifying tool offsets. Additionally, cleaning the spindle and ensuring proper lubrication of moving parts are critical. These steps prevent wear, reduce downtime, and maintain precision in machining operations, ensuring the machine operates efficiently and safely over time.
8.2 Upgrading and Servicing CNC Components
Upgrading and servicing CNC components is essential for maintaining machine performance. This includes replacing worn parts, updating control systems, and servicing motors. Regularly check and replace tool changers, servo motors, and spindle units. Timely upgrades prevent obsolescence and ensure compatibility with new tools or software. Always consult the official manuals and follow manufacturer guidelines for safe and effective servicing.
This concludes the CNC machine manual. For further learning, refer to recommended manuals and online resources for advanced techniques and troubleshooting to enhance your CNC machining skills and applications.
9.1 Summary of Key Concepts
This manual covered essential aspects of CNC machine operation, including safety protocols, programming basics, machine setup, and troubleshooting. It emphasized understanding G-Code, tool radius compensation, and advanced machining techniques. Regular maintenance and adherence to safety guidelines were highlighted to ensure optimal performance and longevity of CNC milling machines. These concepts provide a solid foundation for operators to master CNC machining processes effectively.
9.2 Recommended Manuals and Further Reading
For deeper understanding, refer to the GSK928MA CNC System Operation Manual and Haas Programming and Operation Manual. Additional resources include SINUMERIK Operate Programming and Operating Manual for milling machines and the Centroid M-Series Mill Operators Manual. These manuals provide detailed insights into G-Code programming, machine setup, and advanced machining techniques. They are available online and are invaluable for refining CNC machining skills and staying updated with the latest technologies.